AeroDesign
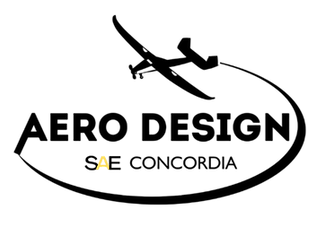
The Concordia SAE Aero Design team is a student-run group that competes in the SAE Aero Design Collegiate Design Series organized by SAE International. These are extremely competitive events that are held annually, with universities from around the world competing with RC Aircrafts designed, manufactured, and tested by students. The primary goal is to develop a cargo lift remote control airplane that can lift specific types of payload. This project allows students to learn about flight dynamics, aircraft configuration selection, detailed design, structural analysis, propulsion, telemetry, and electronics. Members learn responsibility, time management, commitment, and teamwork.

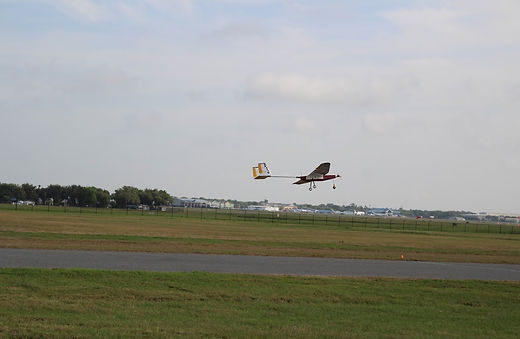
Competition History
Competition in Orlando, Florida - 2015
-
Regular Class 3rd place overall
-
Advanced Class 2nd place overall
​​
​​
​​
Competition in Lakeland, Florida - 2018
-
Regular Class 17th place overall
-
Advanced Class 7th place overall
​​
​
Competition in Orlando, Florida - 2020
-
Micro Class 12th place overall
-
Regular Class 10th place overall
-
Advanced Class 5th place overall
​​
​​
​
Competition in Lakeland, Florida - 2023
-
Regular Class 8th place overall
-
Advanced Class 3rd place overall​
​2017 - Competition in Fort Worth, Texas
-
Micro Class 21st place overall
-
Regular Class 11th place overall
​​
​
2019 - Competition in Fort Worth, Texas
-
Regular Class 9th place overall
-
Advanced Class 8th place overall
​
​
2022 - Competition in Forth Worth, Texas
-
Regular Class 18th place overall
-
Advanced Class 11th place overall
​​
​
​
​
2024 - Competition in Lakeland, Florida
-
Regular Class 3rd place overall
-
Advanced Class 2nd place overall
Aerodynamics
The Aerodynamics team has as its most basic goal ensuring that the aircraft can fly. Other goals of the aerodynamics team include guaranteeing that the aircraft can takeoff in the required distance, ensuring the stability of the aircraft in flight, both static and dynamic and optimising the efficiency. The members of this team achieve those goals by carefully designing the wings, the empennage, and all the control surfaces. The two main design tools used are XFLR5 and OpenVSP.

Team Subsystems
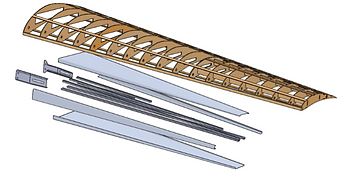
​​Structures
The Structures team’s fundamental task is to ensure the structural integrity of the aircraft. The structures team interacts with the whole aircraft, as every part needs to be analysed to verify that it can withstand the loads acting on it. Another aspect of structural design is weight optimisation, the weight has to be minimized and also well distributed throughout the aircraft to achieve balance. The members of the Structures team work extensively with Solidworks, as they are in charge of creating the CAD model, but also use other analysis tools to perform FEA. ​​
Systems
The Systems team is tasked with designing the flight control system as well as the propulsion system. The work entails sizing the electric motor and the propeller, selecting the servomotors, along with the battery. In addition, ensuring that the electronics within the aircraft can communicate effectively with the controller is also a big part of the work. The members of the Systems team are also working on a research project which will record flight data.
